Our Clients

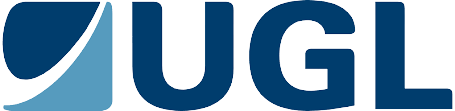
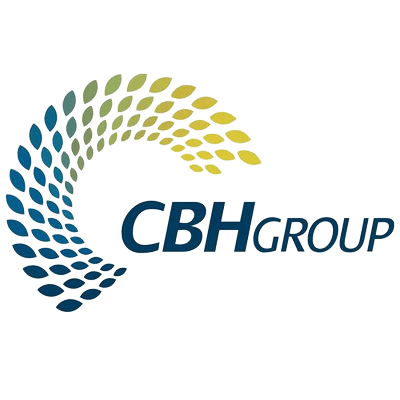
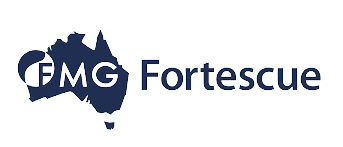
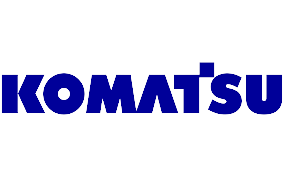
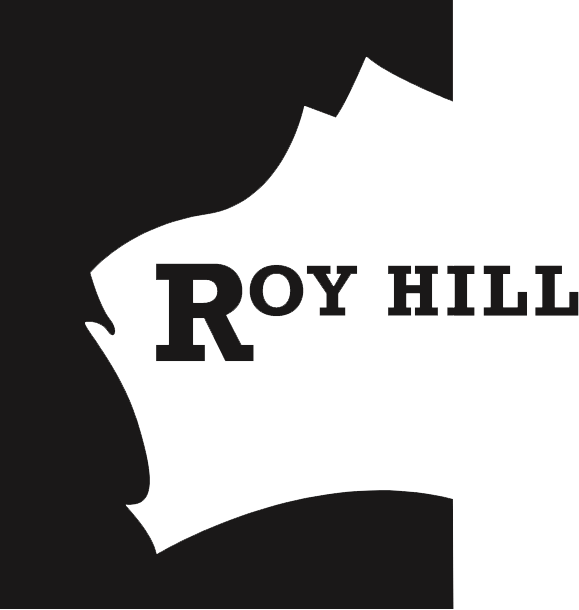
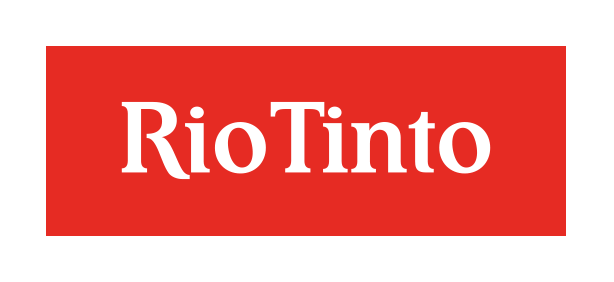

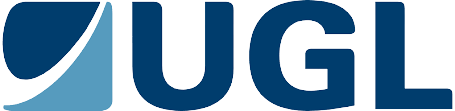
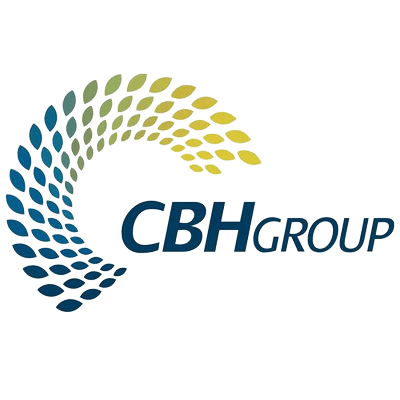
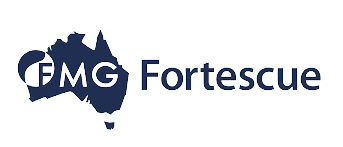
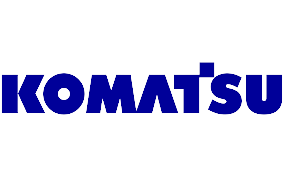
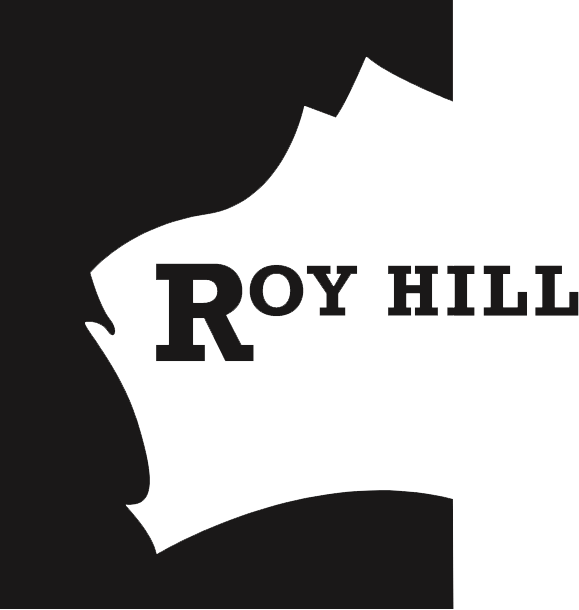
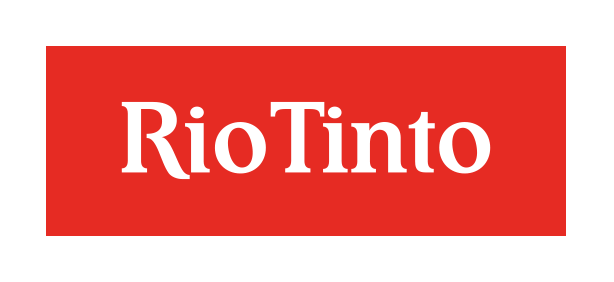

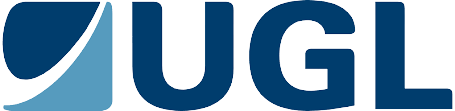
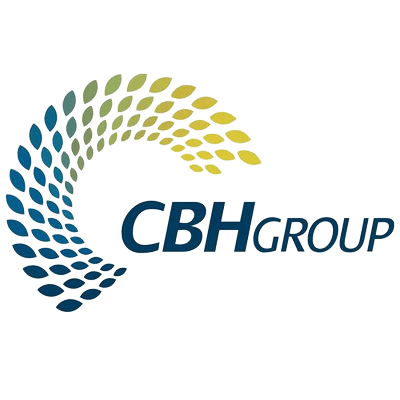
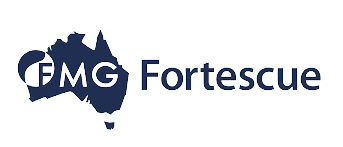
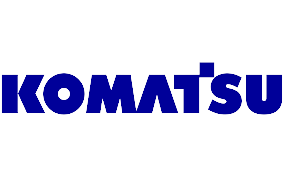
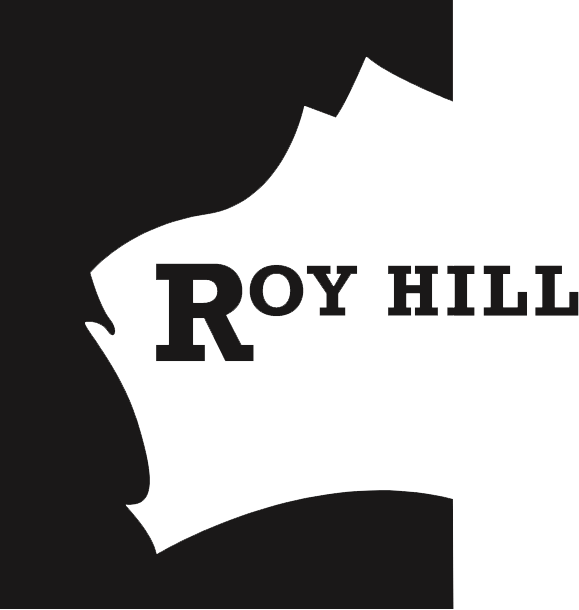
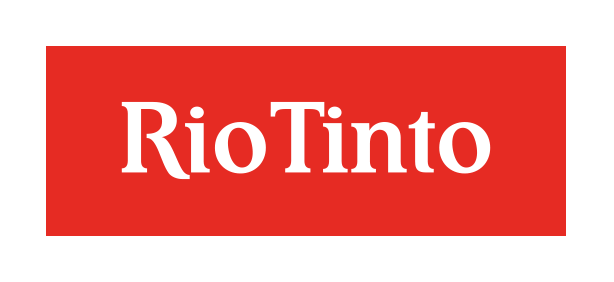
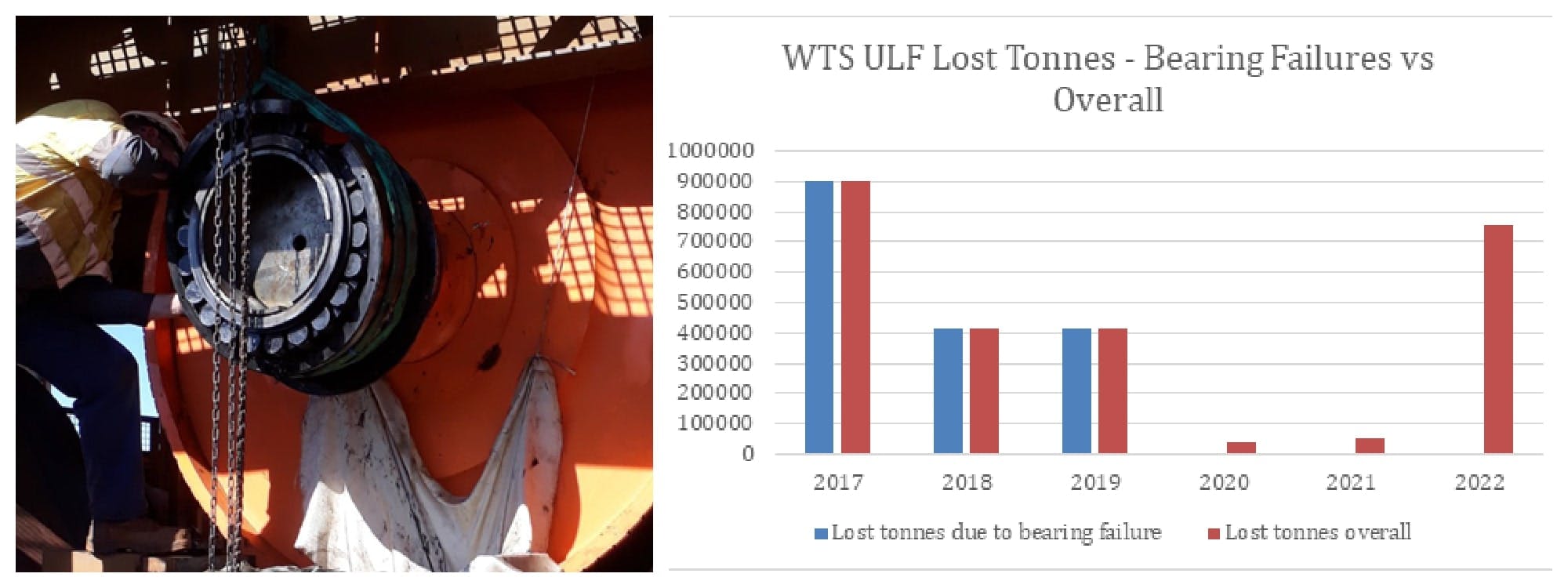
Figure 2: total lost tonnes due to bearing failures - zero bearing failures since 2019
Challenge:A major iron ore miner in Western Australia's Pilbara region faced a critical issue: chronic conveyor pulley failures on their vital 23km overland conveyor system. These failures caused significant downtime, leading to lost production and revenue. Initially engaged for bearing failure analysis in 2017, DASH Engineering discovered the culprit: inadequate labyrinth seals allowing contamination ingress (iron ore and water) into the bearings.Impact of Failures:The consequences were severe. Each unplanned downtime event, caused by a catastrophic bearing failure, resulted in up to three days of lost production, incurring an estimated cost of $18 million per failure.Uncovering the Root Cause:DASH Engineering's investigation revealed that even perfect housing alignment and adjustments to grease feed rates offered minimal improvement. The core issue was contamination migration: labyrinth seals allowed contaminated grease to enter the bearing housing, causing rapid wear and failure.Developing a Superior Solution:Understanding the limitations of existing seals, DASH Engineering was challenged to develop a more effective solution. The result? The innovative SAPO® seal, designed to address the specific challenges of this application.The SAPO® Seal: A Game ChangerThe SAPO® seal represents a breakthrough in conveyor pulley reliability. It departs from traditional labyrinth designs by offering several key advantages:
- Superior Contamination Protection: Effectively blocks the ingress of dirt and water, extending bearing life and minimizing downtime.
- Accommodates Misalignment: Adapts to inherent system misalignment, a common cause of bearing failure.
- Bearing Float Capability: Allows for axial movement of the bearing, a critical factor in conveyor pulley applications.
- Monitorable and Maintainable: Utilises a pressurised closed-oil system for easy monitoring, flushing, and oil changes while operational.
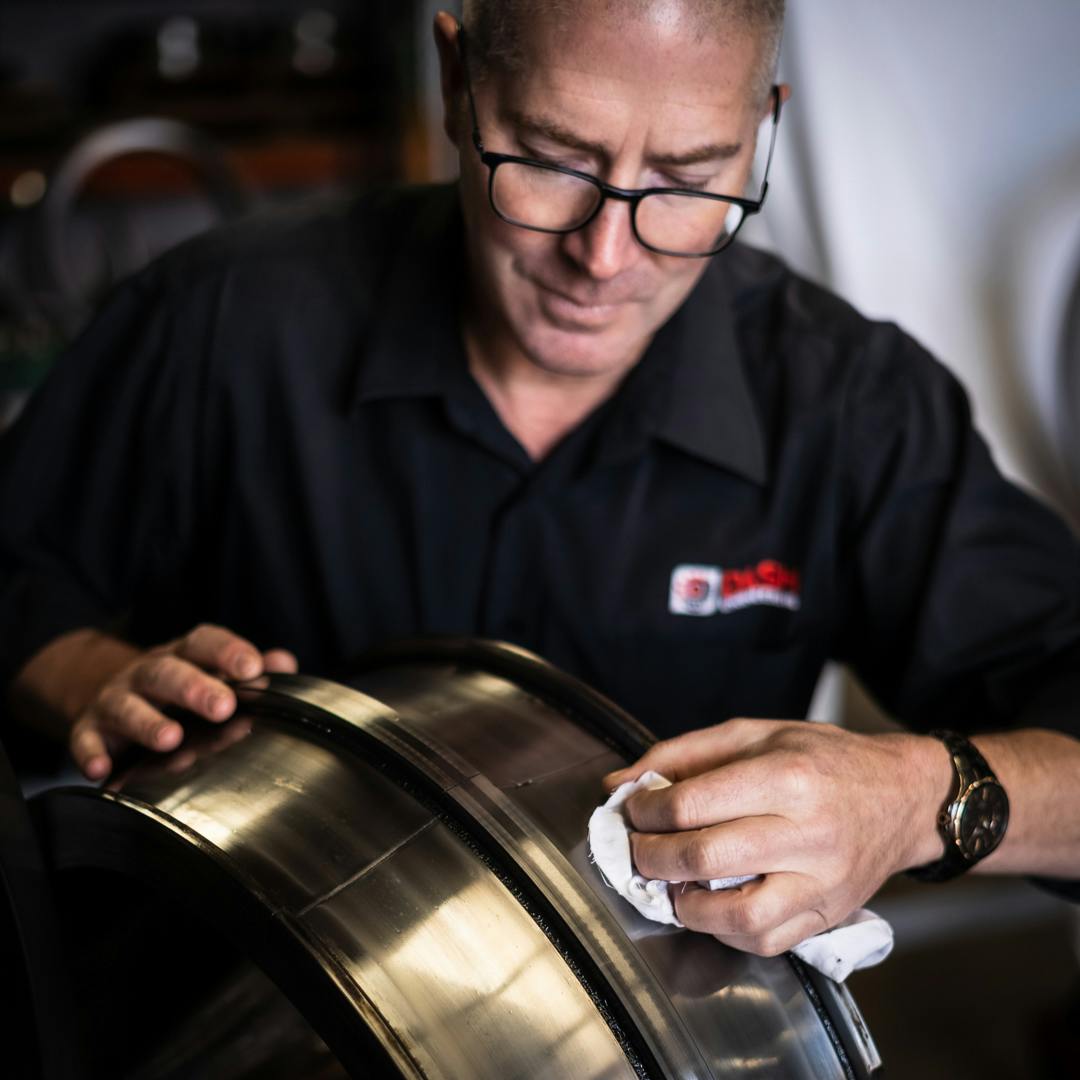
Contact Us
Call or email us today or leave us a message and we'll get back to you soon!